With the development of the global economy and the acceleration of industrialization, ABS resin, as an important engineering plastic, has been widely applied and driven by demand.
The emergence of ABS injection molding technology has demonstrated the perfect integration of material science and industrial manufacturing, becoming a classic choice in manufacturing processes.
Material Characteristics
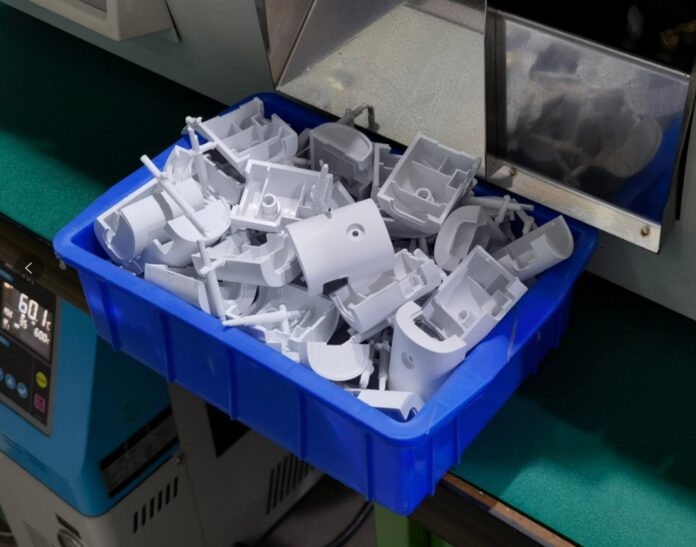
ABS stands for Acrylonitrile Butadiene Styrene. This plastic material consists of three monomers, each of which provides its own properties to the polymer plastic, giving it a wide range of properties.
Acrylonitrile offers properties such as chemical resistance, hardness and heat resistance, while other properties include impact resistance and toughness from butadiene, and strength and gloss from styrene.
ABS resin is an amorphous, opaque, non-toxic, tasteless, light-yellow thermoplastic resin with the following characteristics:
It can be molded at temperatures above 160°C and only starts decomposing at temperatures above 270°C.
Its density ranges from 1.04-1.0g/cm³, and it has medium flowability.
ABS raw materials are hygroscopic and need to be thoroughly dried before molding. The moisture content should be controlled below 0.1%.
It has good mechanical and thermal properties, high hardness, and is easy to plate with metals on the surface.
Exhibits high fatigue resistance, stress-crack resistance, and impact strength.
Resistant to acids, alkalis, and other chemical corrosions.
It is affordably priced, easy to process, mold, and modify.
The double bonds in butadiene are susceptible to oxidative degradation when exposed to ultraviolet light, resulting in poor weather resistance. Its heat resistance is not ideal, with an operating temperature range of -40 to 100°C.
Product & Mold Design
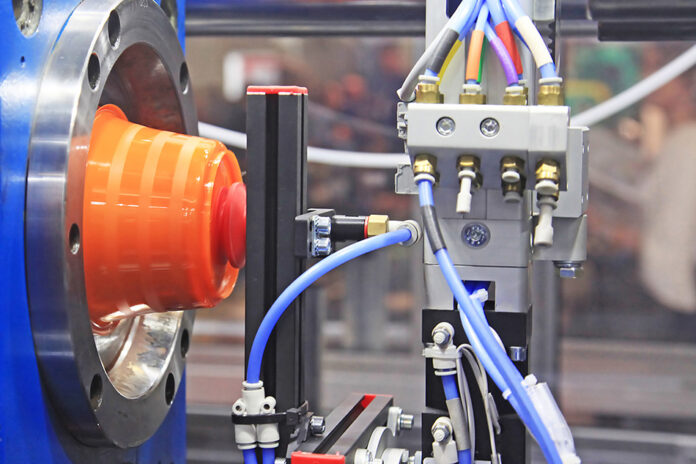
The product’s wall thickness is associated with the melt’s flow length, production efficiency, usage requirements, and more.
It should be as uniform as possible, with no variations exceeding 25%. The ratio of radius to wall thickness should not be less than 0.3.
Typically, ABS molds for ABS injection molding have a thickness ranging from 0.025mm to 0.05mm.
To prevent issues like poor exhaust, resulting in melt burns and obvious seam lines during the mold filling process, it is necessary to create exhaust holes or exhaust grooves with a depth no greater than 0.04mm. This facilitates proper gas discharge.
To ensure efficient filling of the entire mold cavity with ABS melt, the runner’s diameter should be at least 5mm. The gate thickness should exceed 30% of the product thickness, and the length of the straight part entering the cavity should be around 1mm.
The gate’s location should be determined based on product requirements and material flow directions. For plated products, the gate should not be placed on the plating attachment surface.
Processing Conditions
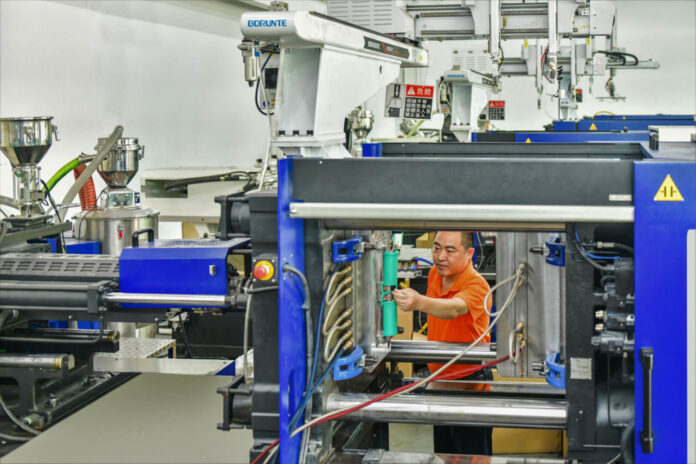
In the ABS injection molding process, strictly controlling the process parameters is of utmost importance and is key to successful molding.
The following are the requirements for the process conditions during the injection molding process:
Drying Process
ABS plastic is highly sensitive to moisture, with a water absorption rate ranging between 2%-7%. It requires thorough drying and pre-heating before processing.
Typical drying conditions are controlled at 80-85°C for at least 2 hours. For products with special requirements (like electroplating), the drying should be at 70-80°C for 10-18 hours (keeping moisture below 0.2%).
Injection Temperature
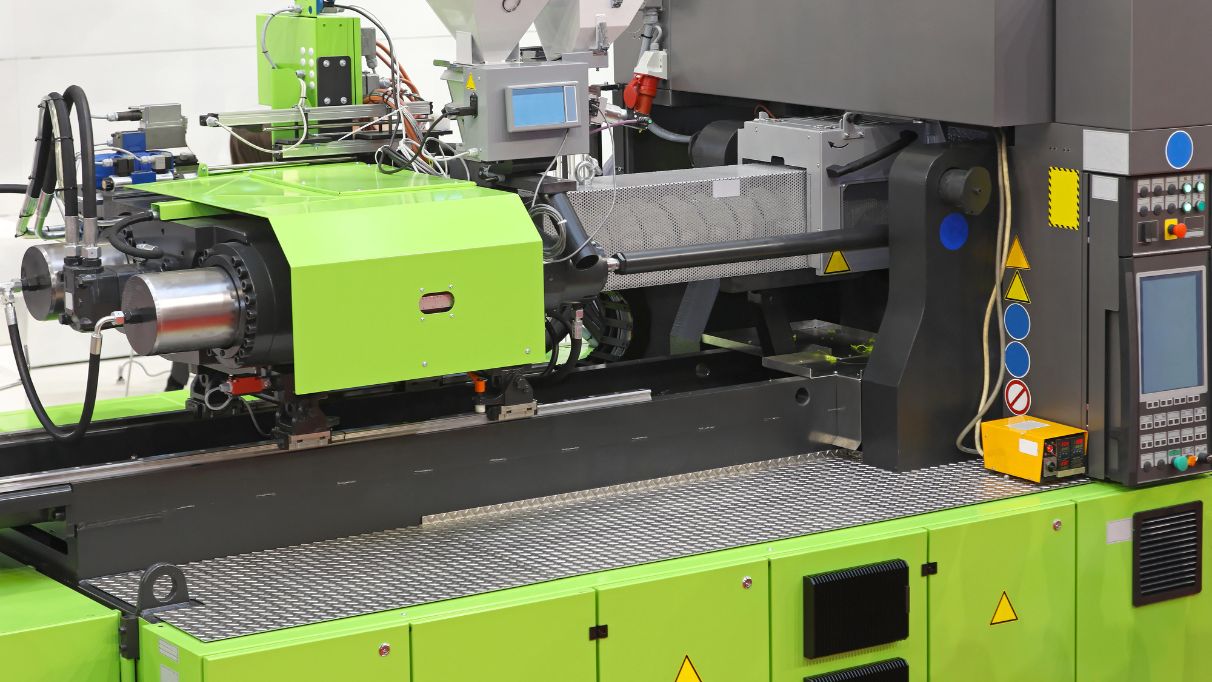
The melt viscosity of ABS resin is less sensitive to temperature. Prolonged exposure to high temperatures can cause decomposition and carbonization, which in turn increases the melt viscosity.
Therefore, the temperature range should be maintained between 210-280°C. (For injection machines, furnace temperature is maintained at 180-230°C; for screw machines, furnace temperature is kept at 160-220°C.)
Injection Pressure
Due to the higher viscosity of the ABS melt compared to polystyrene and modified polystyrene, a higher injection pressure, around 90-140MPa, is utilized.
However, not all ABS products require high pressure. For products with smaller volume, simpler structure, and greater thickness, lower injection pressure can be used.
Injection Speed
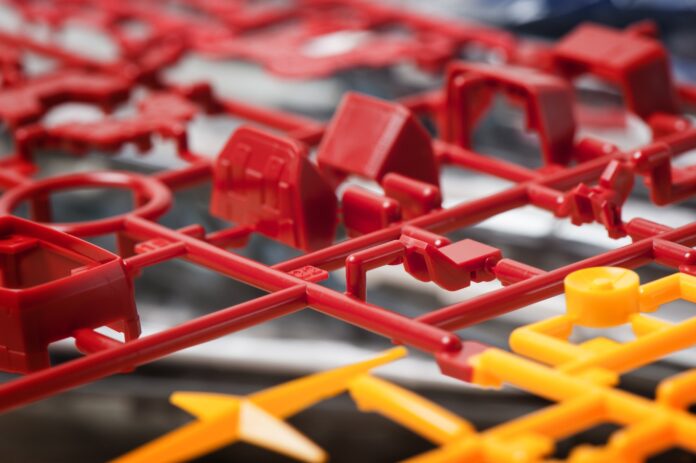
ABS material is best suited for medium injection speeds. When the injection speed is too fast, the plastic is prone to scorching or decomposing, releasing gases, leading to defects like weld lines, poor gloss, and red discoloration near the gate.
However, when producing thin-walled and complex components, a sufficiently high injection speed is necessary to ensure complete filling.
Mold Temperature
ABS has a relatively high molding temperature, so the mold temperature is also relatively high. The mold temperature is generally adjusted to 75-85°C.
When producing components with a large projection area, the fixed mold temperature should be 70-80°C, while the moving mold temperature should be 50-60°C. When injecting large, intricately shaped, thin-walled components, consideration should be given to specifically heating the mold.
Advantages
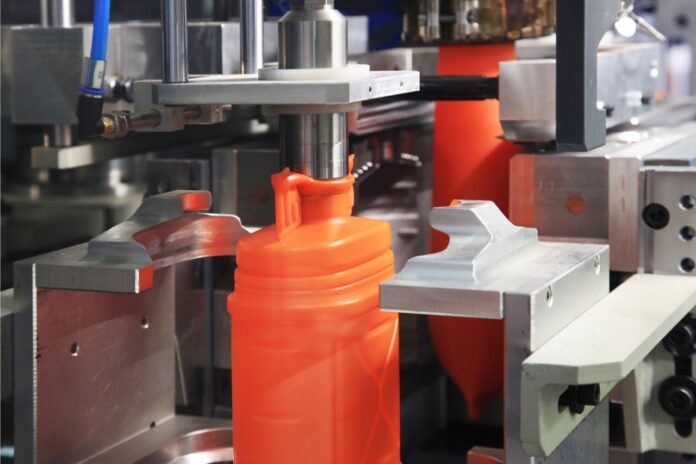
The ABS injection molding process, which can also be described as the rapid automated production of plastic parts, produces parts with a high degree of consistency and accuracy, and fits customer requirements for customized products of specific shapes, sizes and functions.
In addition, the concept of sustainability has made ABS injection molding cost-effective by focusing on the efficient use of materials and energy, and by leveraging the features of efficient manufacturing to meet the demands of mass production.
In the future development of the road, ABS injection molding will continue these advantages, in the manufacturing industry to continue to contribute its strength.
Application
ABS plastic due to the greater mechanical strength and good overall performance, the precision injection molding processed ABS injection molded parts are mainly used in automotive, electronic appliances, building materials and other fields.
Automotive industry: ABS injection molded parts are widely used as raw materials for lightweight automotive parts, mainly including automotive instrument panels, body panels, interior decorative panels, steering wheels, ventilation ducts and other parts.
Electrical field: ABS plastic has a wide application market in home appliances and small appliances, often manufacturing internal and external parts of electronic appliances such as refrigerators, TVs, washing machines, hair dryers, computers and so on.
Building materials : With high strength and impact resistance, ABS injection molding technology is used in the building materials industry as the production process for ABS pipes, ABS sanitary ware, and ABS decorative panels.