Producing various parts isn’t always the work of heavy machinery; there are multiple techniques which people use. These techniques make enhancing the mass-scale production of different machinery parts easier. So in this article, let us discuss a process known as chemical etching and learn about its procedural implementation in creating the final product.
What Is Chemical Etching?
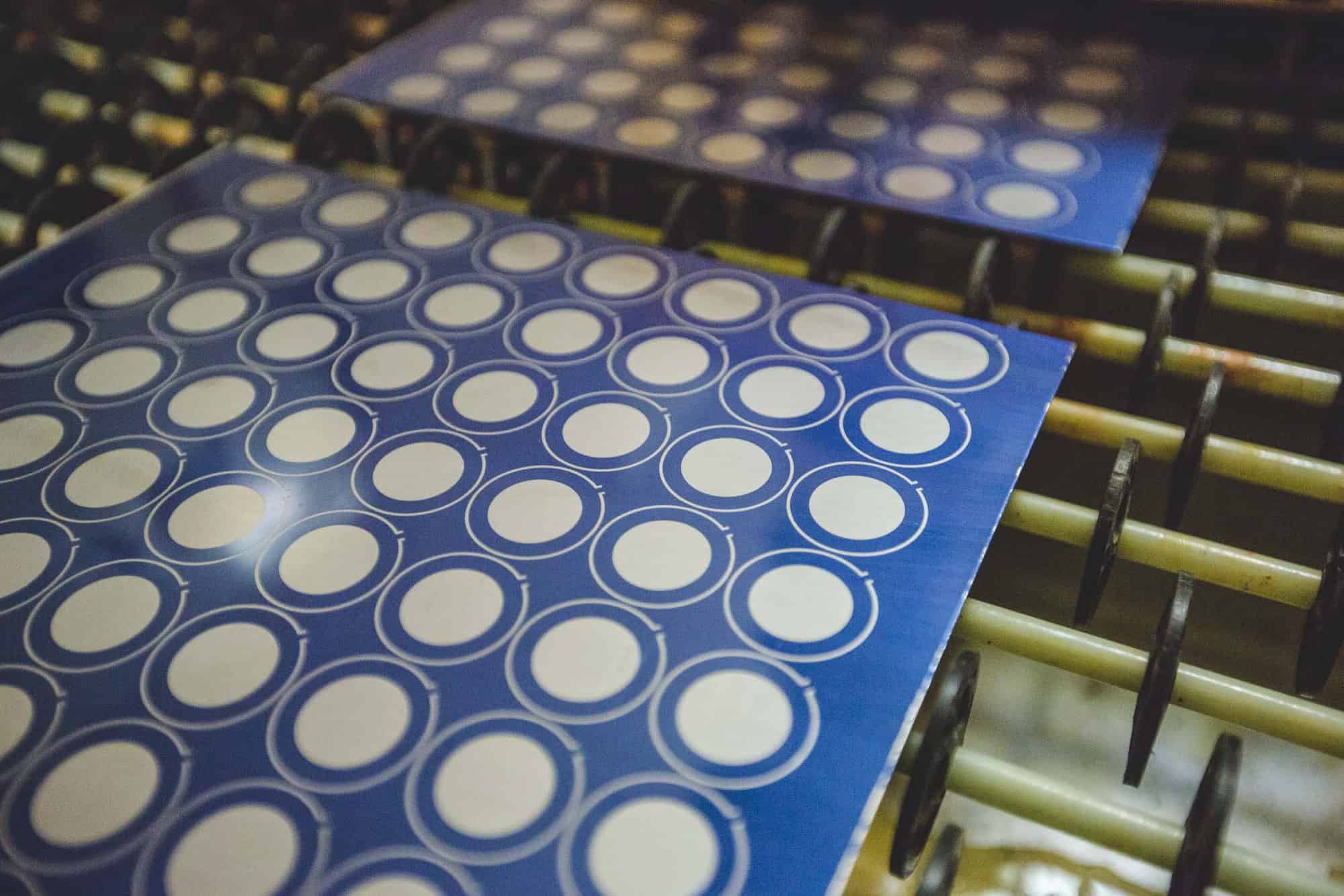
Chemical etching is a process which involves the use of chemicals by well-trained experts to etch various non-required parts of metals from a great shape metal. The desired shape is stored in the system and then photo-pasted on the metal sheet. The non-critical part is removed from the sheet to ensure that the final product meets the requirements. The process of chemical etching is limited only to a given number of metals and alloys.
Procedural Implementation Of Chemical Etching
The process of chemical etching is completed in a series of steps, which are listed and discussed below in detail. In the last phase, the well-trained experts and professionals calculate all the variable factors influencing the final product’s etching time and thickness. You can find here the best chemical etching services in the industry.
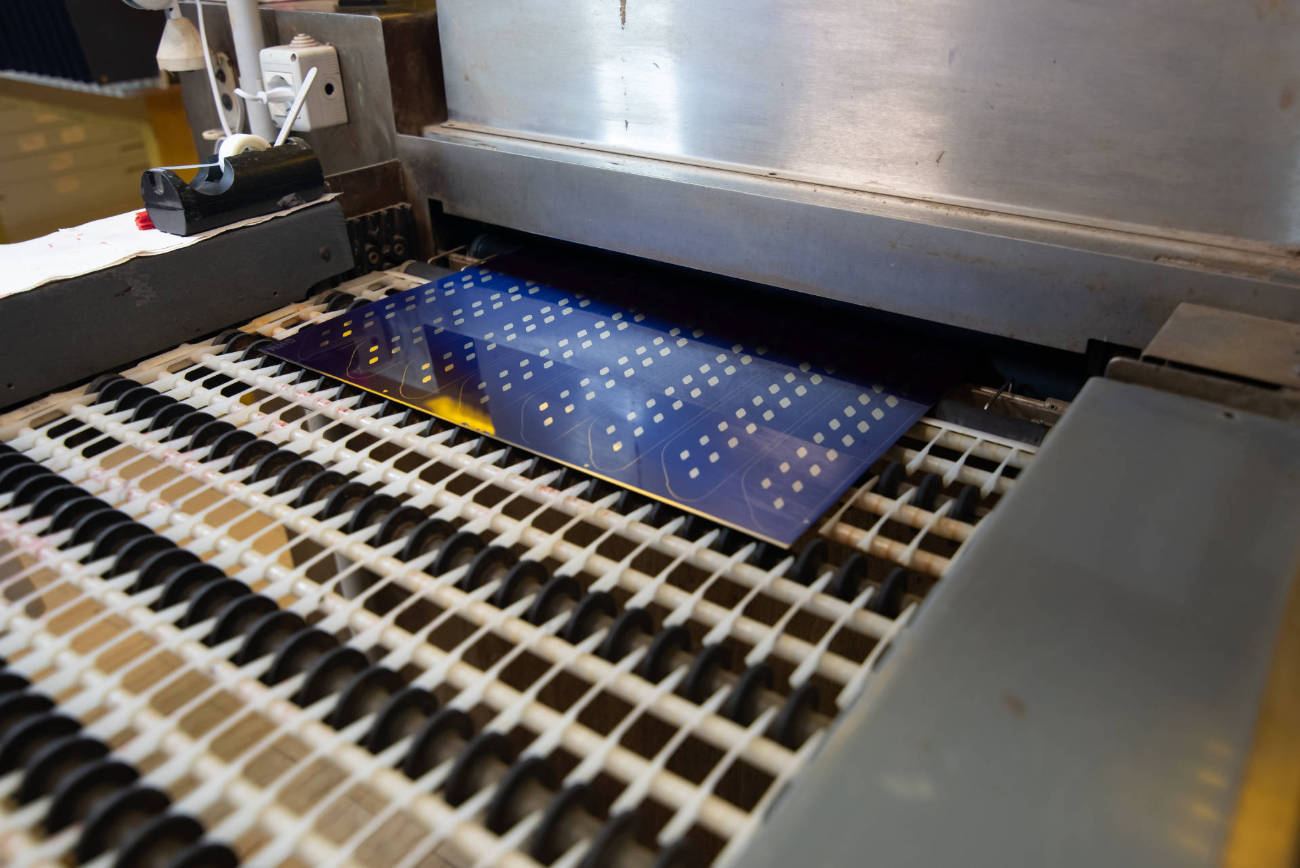
Choose Material
The first thing to be kept in mind is choosing the perfect material for the purpose. Each material has internal links and contact with other atoms, which defines its tensile strength. So all the different parameters regarding the perfect cut from the entire metal would depend on the quality of the metal. The thickness of the metal depends on various sheets placed over each other, and some products contain different layers, with each layer made up of different metals.
Cleaning
The primary issue with the chemical process is that it reacts with various debris and dirt present on the metal, so you need to make sure that the metal is perfectly clean. In the entire process, you also need to ensure that the cleaning product does not react with the metal. Oil stains cover the surface in various instances, so multiple products are used to get rid of them. Once the surface of the metal is cleaned thoroughly, you must wear gloves to manage it, as sweat and oil in your palms could get imprinted on the surface.
Lamination
Once the surface has been cleaned thoroughly and stored in a clean place, you must place a lamination layer over it. This layer should have unique features, including a photoresist surface placed in the region that doesn’t need to be etched. The etched area is exposed, and in such instances, the non-etched part is protected from the powerful rays using this lamination. This lamination occurs on both sides of the metal sheet.
Printing The Shape
Once the cleaning has been done thoroughly and the photoresist layer is placed on both sides of the sheet, a critical part of the process comes. In this part of the process, the final product’s design is stored in the form of a photo and is embedded in a photo tool. This photo tool utilizes highly charged UV rays to cast this photo image on the metal layers. This photo image is placed on both sides of the sheet, making it easier to etch the non-critical part easily.
Developing
Once the photo layer is placed on the metal surface, the shape is imprinted on the metal sheets. The part of the metal that wouldn’t be covered with the photoresist film will dissolve in this process. The remaining amount left would be the shape of the final product. The photo film cross-linked section would be visible after being developed, which makes things easier for other products.
Etching
In this part of the process, chemicals are used, and then proper time is given for the metal to etch for the final design. People use the etchant spray to place in etch chambers for further work. These chemicals, like Ferric Chloride, are prepared for chemical baths to eliminate extra metal. Well-trained professionals and technicians monitor the entire etching process because variable factors like thickness, size, temperature, concentration and a lot more are considered. The metal type also plays a crucial part in determining the etching time of the sheet.
Stripping
Once the etching process is completed, the final metal sheet is brought out of the chemical bath. Now that the final shape is attained, you must remove the photoresist film from the surface, and the bare metal should be exposed; when the photoresist film is released, a shining metal surface is obtained at one end.
Get The Shape Right
Once the final product is attained, the task is to check the dimensions and thickness of the metal layers. So this process involves using optical instruments, making it easier for people to look through the final product from various angles. The final product involves factors like thickness, metal size, metal type and a lot more. This equipment uses laser techniques even to develop the 3D model of the development in the system.
Final Product
Once the shape is attained, you must start working on finishing the product’s final look. Such processes as electropolishing ensure that the metal is in the best condition. Various tests are performed to ensure no cracks in the final product, and with heat and Wire EDM treatment, the entire process comes to a halt.
Advantages Of Chemical Etching
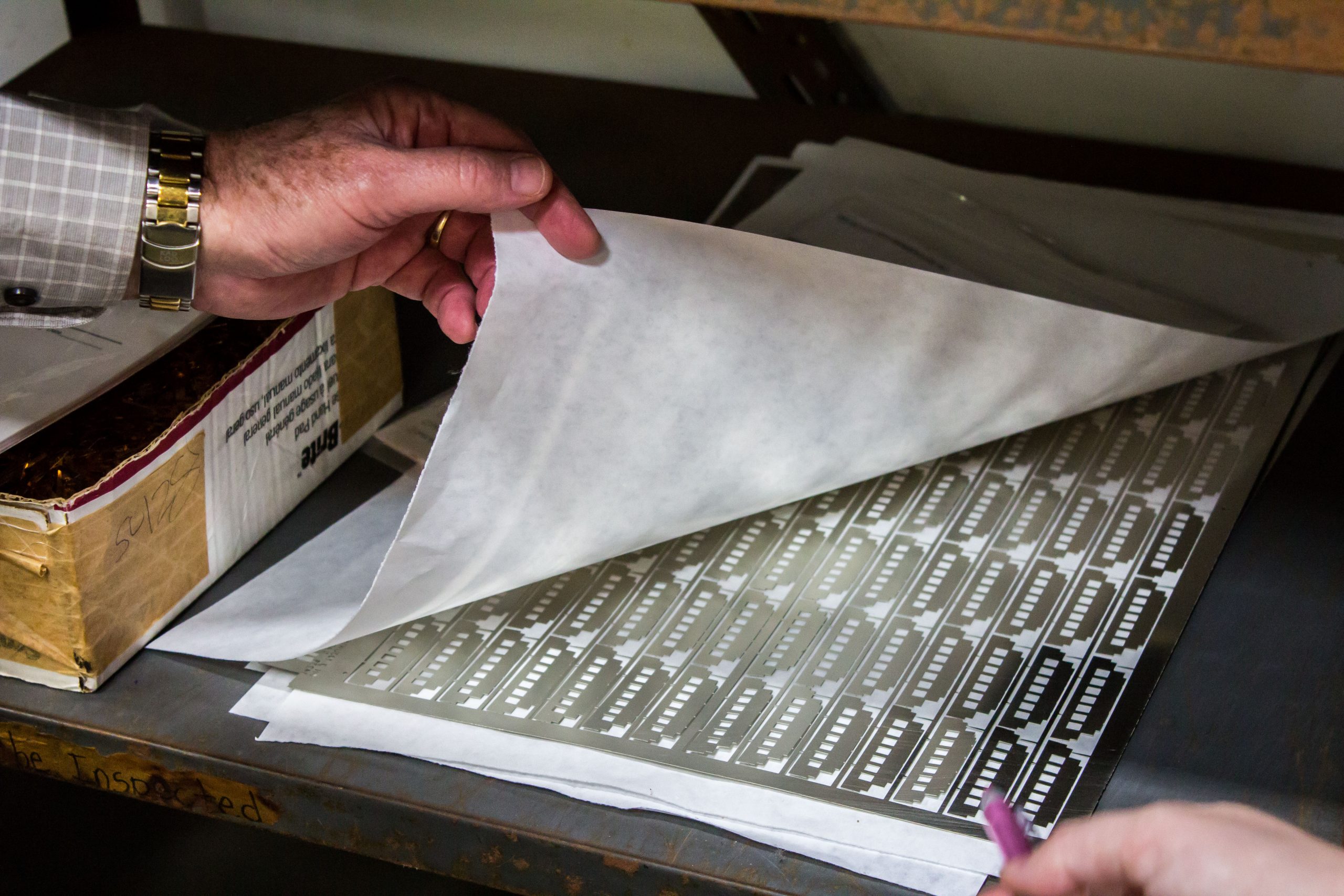
The process of chemical etching turns out to be an efficient decision compared to other methods, and significant reasons influence the decision.
- Consistency and control are essential because the metal has high tolerances, and in such instances, it’s tough to focus on small values and variables. With chemical etching, it becomes easier to manage these values efficiently.
- This process is an economically efficient decision as it makes it easier for people to cut down various machines and utilization costs over the long term.
- Process precision and efficiency are core features which reduce the number of faulty final products making it easier to reduce the number of losses.
- This process is suitable for mass production as users can produce various parts in bulk.
Conclusion
The process of chemical etching involves using well-trained professionals with proper knowledge and experience in the field. The variables like temperature and concentration are manipulated to receive the final product. So in this article, we discussed this procedure in detail.